AyMINE – Technical documentation
Modules
Integration with ERP Abra Gen
Task, project & quality management
Manager approval with the task report
Why some data can't be deleted
Adminitration of areas, projects, calendars
Region / project / methodology
Change management process in a project
GDPR and record of qualifications
Qualification of user or contact
Right to Manage Qualifications
Failure Analysis for an Individual Property of a Component or Process
FMEA – Probability of Detection
FMEA – Probability of Occurrence
Task, project & quality management
Administration of the Task Management Module
System rights for the task management module
Improvements and Preventive Measures
Methodology and Quality Management systems
What a methodology / QMS consists of
Problems, tickets and their management
Collaborative Resolution of Multiple Problems
Customer Service Response Generation
Incident and Quality Issue Management
Objects affected by the problem
Problems, Incidents, Helpdesk Tickets
Return project plan by baseline
Sample tasks and methodologies of the area
Effect of the task on the right to modify the attached object
The person responsible for the task
Working procedure – task definition
Management of responsibilities - RACI Matrix
Objects related to the task pattern
Contacts and directories module (CRM)
Order overview for customer groups
Contacts and directories module (CRM)
System Permissions and CRM Module Settings
Send bulk messages in compliance with GDPR
How to correctly forget a person's details
Unsubscribe and set preferences
for bulk mail
Web management and automation
Receiving a message from the web
Human resources
Personalistics – User Permissions and roles
Human Resources module security
Manage department / division data
Overview of Personnel Information for pracov# Employment Contract
Synchronizing staff and system users
Products, assets and sales
Manage the Property & Business module
Why are the Quality criteria usefull
Received order for goods or services
Managing Finance
Metrics and Measurements
Work summaries from generated data
Technical Modules
Sabre plugin module
Enterprise Architect connector
Database link to Enterprise Architect database
Enterprise Architect connector
System Modules
The AyMINE Framework Module
AyMINE — Tips for Mobile Usage
Configure how your system looks and works
Gestures and Keyboard Shortcuts
More about how the system works
Private notes and tags for objects
Overview of Modules and Record Types
Filtering in the list of records
System Management
Additional functions with files
Copying and moving files between objects
Files (documents) linked to the object
Formatted texts in the application
Gateway settings for external messages
IMP gateway settings for email communication
Internet Call Gateway Settings
Message with the outside world
HARA for product
Hazard & Risk Analysis is the initial step in the decision-making process to classify a product in the safety class. System support helps you to make and document the analysis and its progress
- HARA or FMEA?
- How to carry out HARA analysis
- Why system support is useful for HARA
- You may be interested
The results of HARA analysis are crucial for assessing whether a product can be developed in the "normal" quality control mode (QM-level) or must be developed according to one of the ASIL A-D or SIL levels (depending on the type of standard; further, for simplicity, common (A)SIL)
HARA or FMEA?
HARA and FMEA both work with similar concepts and product ratings, but their basis is fundamentally different. The fundamental difference between HARA and FMEA is at the time of implementation and the detail of the analysis. In terms of the HARA processing process, it corresponds to the HAZOP (Hazard and operability study) standard.
HARA analysis is performed in a project at the very beginning, when its detailed analysis is not known. The basis of the assessment is therefore its potential operational impacts.
Within HARA analysis, the key question is: What is the risk that may arise from the part under consideration?
FMEA analysis is carried out on the basis of a detailed analysis and is based on the possible failures of the individual components and components that make up the product under consideration.
The key question of FMEA analysis is: What may break down and what may cause it?
For FMEA and HARA, the common point for the analysis is that the assessment is carried out in the context of
- Assessment of the risks caused. Example: Serious injury risk
- Risk assessment based on the assessment of how often the conditions occur when the threat may occur. Example: Driving/operating at night
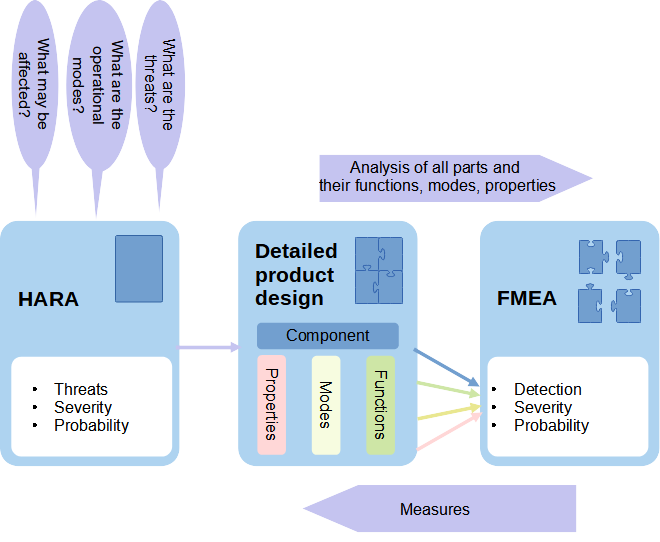
How to carry out HARA analysis
The HARA analysis is described here on the basis of ISO 26262-3. However, the procedure is identical for other standards, e.g. Mil Std 882D.
The basic steps of HARA analysis are
- Identification of the product for which HARA analysis is carried out.
- Description of the environment in which it is used, especially what is in its surroundings and may be affected by the product
- Operational modes in which it is used and the frequency of the given threat
- What threats it may cause in each mode
- Overall assessment (rating) of the threat given by the product of the threat, the probability of the situation
The result of the analysis is
- Proposals for measures that reduce threats
- Classification in ASIL / SIL safety class (Depending on the type of standard used)
Measures must have practical outcomes
Measures must have practical outcomes in order to make sense, they must be translated into specific requirements that the design meets. A typical example of a measure is:
Redundancy
Redundancy is the duplication of an element that may fail.
The most obvious example is car lights, which are duplicated even with much internal logic. Redundancy is used more than it seems at first glance. It is not just flashing lights in the mirror (duplicating the front flashing lights) but e.g. independent sensors, calculating values from other data – e.g. combination of data from other sensors, etc. Duplication is also used for indicators reporting a problem to the driver.
Safety mode
The basis of the safety mode is the recognition of a fault, potential fault or risk of a fault occurring and switching to the safety mode.
An example of a safety mode is a reduction in the power output of an electric car engine when the battery temperature exceeds a specified threshold.
Increase in reliability
Increased reliability means the use of materials, parts and manufacturing processes that are less likely to fail. Reliability is important for all 3 basic parts – HW / SW / ME (hardware, software, mechanical parts).
As banal as it sounds, increasing the reliability of a part is definitely not banal. Examples are
- For hardware: use of components with higher protection against elmgmt. interference, temperature resistance, etc.
- For software: use of secure programming rules, guaranteed libraries and the simplest possible code
- Mechanical part: More durable materials, more accurate mounting
I don't know.
Of course, the various exit checks apply to all cases together.
Why system support is useful for HARA
Technically, the main output of HARA is the analysis of the thought process in particular. However, HARA's analysis, like FMEA's, does not stand alone, but is made in the context of the whole project it influences and fits into:
HARA Documentation
- It must be documented who participated in the analysis
- Explicit requirements for HARA review (must be independent) so both investigators and reviewers of the analysis must be documented
- There must be evidence that it actually took place – e.g. according to ISO 26262 it should be controlled by a process control system
- Requirements must be reviewable – there must be a rational justification for them to actually help
Material coherence
- Every HARA measure becomes a safety requirement for the product or production process
- Safety requirements must be part of the traceability system and documented from their inception to their implementation
- Traceability is reciprocal – it must also be possible to trace back the reasons behind the HARA analysis that led to the decision to create the requirement.
With HARA system and process support in AyMINE, you will not only have quality documentation, but also interdependence with the product documentation and the project. And also process support.